The beginning of the 21st century, the orthopaedic world saw a new era as
enthusiasts started developing new approaches to osteosynthesis.
Among them, Grégoire Larché, Jean-Pierre Podgorski and their teams have worked tirelessly at Newclip Technics
to design innovative fixation systems, specific implants and new solutions using modern technologies.
Their ambition remains to contribute to the efficiency of the surgical procedure, for the best possible patient benefit.
For more than twenty years, joint preservation, but also repairing bone fractures,
are the two leitmotivs of the company to participate in the return of mobility to the patient.
The history of Newclip Technics
From innovation comes movement
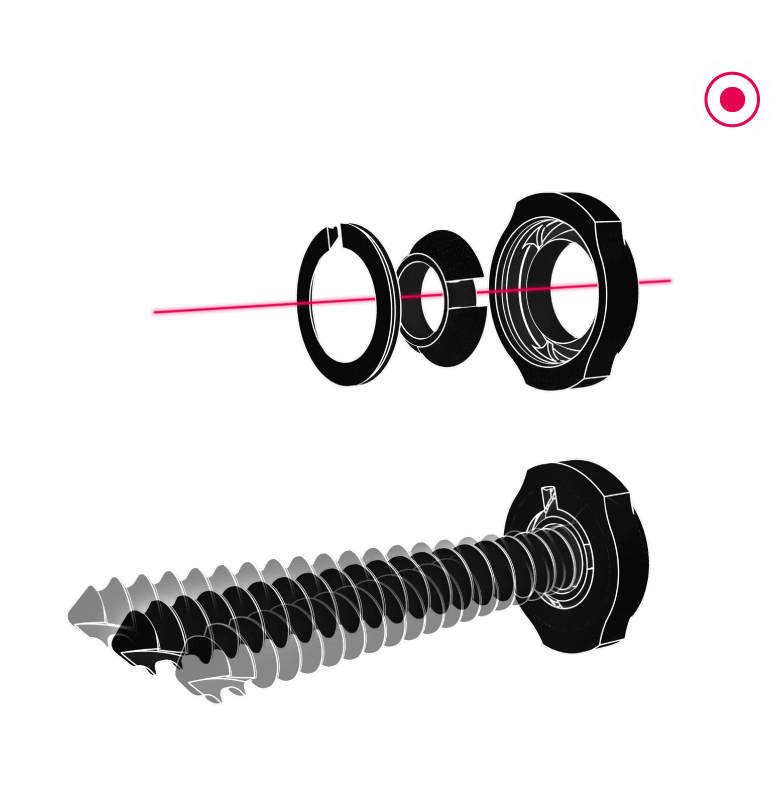
An idea, a vision, a reality
Coming from the world of osteosynthesis, the founders of Newclip Technics initially wanted to improve the fixation system for locking plates. They worked on a technology to combine polyaxiality and locking of the screw to the plate. In 2001, the first polyaxial locking screw-plate fixation system called DualTecSystem (DTS) was created and patented.
This innovation was rewarded during the French Ministry of Research competition and allowed its launch and development on a larger scale. The idea then became a reality, and Newclip Technics assumed its status as an independent French osteosynthesis manufacturer, based in the region of Nantes.
In 2002, the first range named Atlantic was released, consisting of knee osteotomy implants incorporating the DTS system.
A new horizon: the upper limb
From the success of the lower limb, requests were made to transpose this know-how to the upper limb. Since miniaturizing the DTS technology was not enough to meet this challenge, it was necessary to develop a more compact polyaxial locking system (known as DTS2) compatible with implant designs adapted to the anatomical specificities of the bones.
The idea of “Bone mapping” was then born. This technique makes it possible to design implants whose bearing surface on the bone takes on the shape of the bone. It also allows an unprecedented congruence of the implant to the bone anatomy, while absorbing the mechanical stresses of the rehabilitation of the patient.
The combination of these different technologies has enabled the creation of other ranges of osteosynthesis implants dedicated to the upper limb, around other joints (elbow, clavicle, etc.).
Launched in 2006, Alians Radius was the first upper limb range introduced by Newclip Technics. Designed for wrist fractures, it will continuously evolve over time and the technologies developed by the company, to become one of the key products, under the current range name: Xpert Wrist 2.4 .
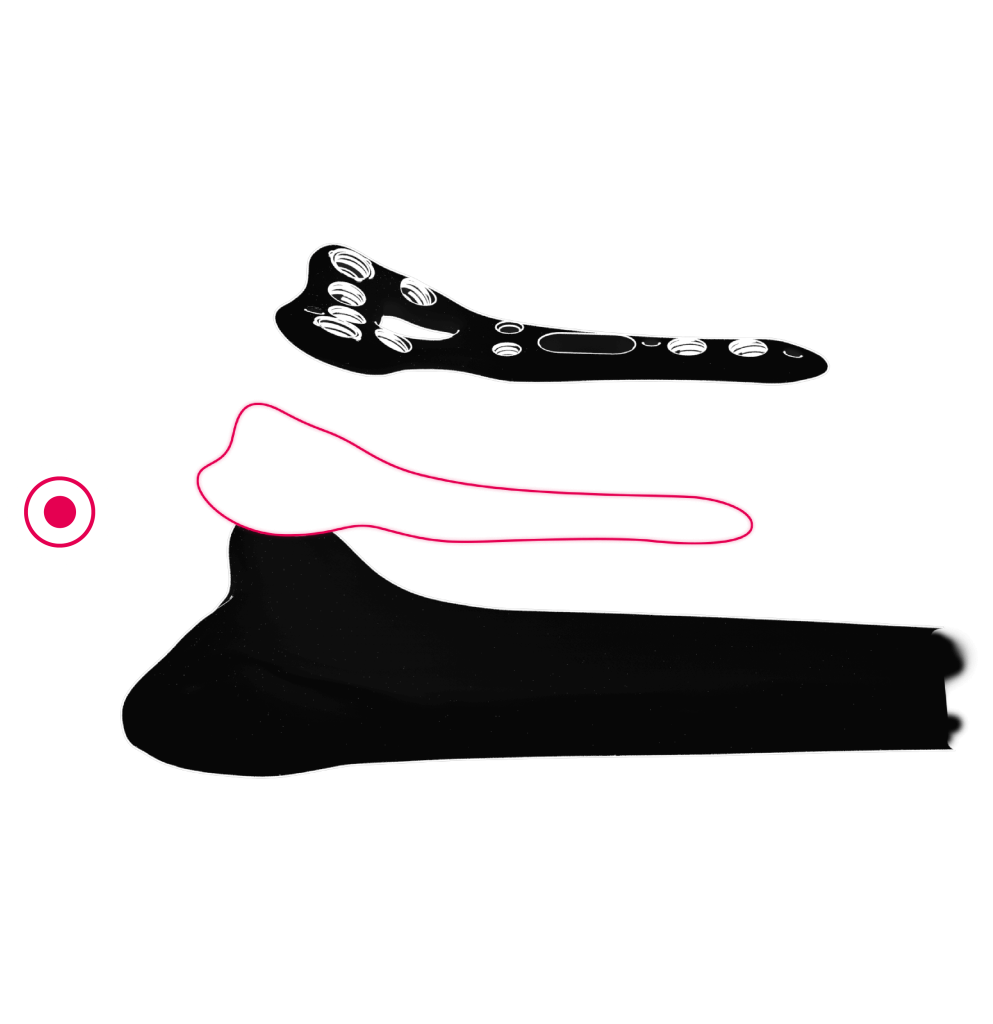
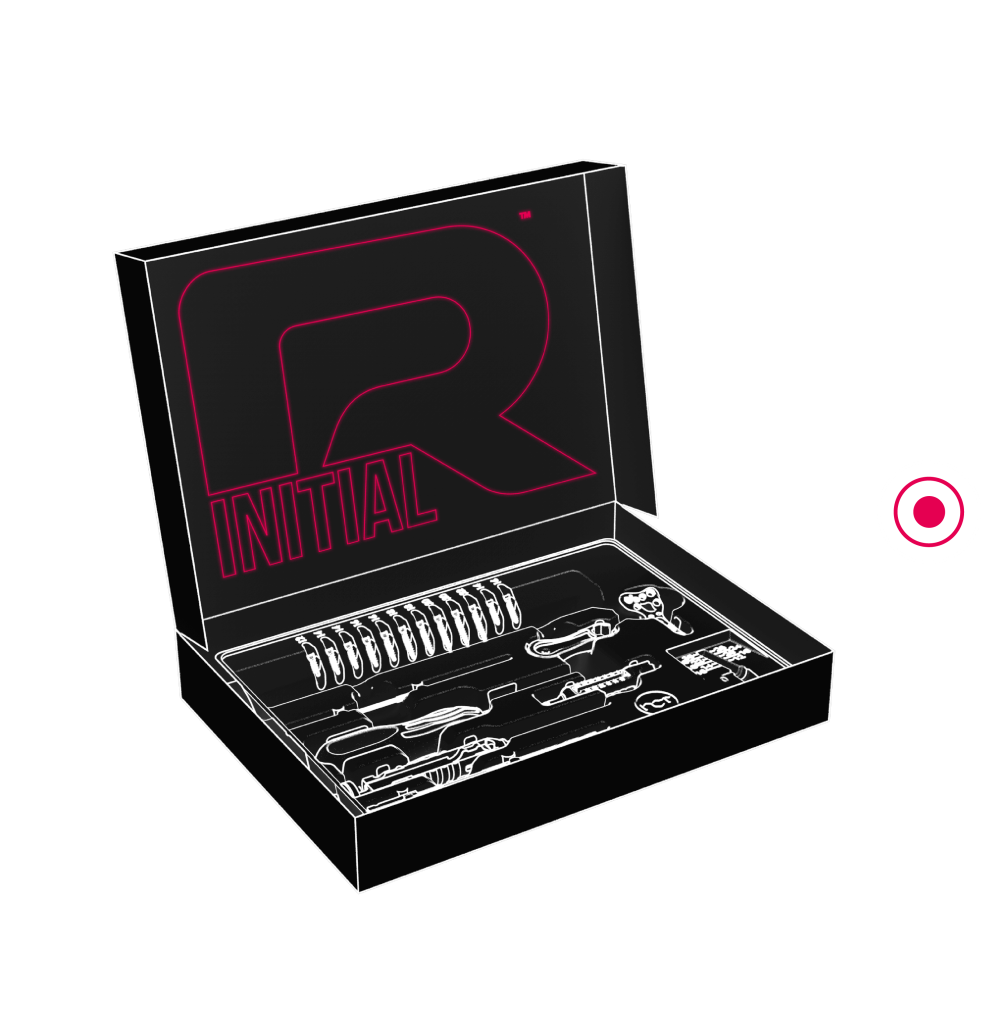
Fresh solutions
Having established its reputation through its fixation systems and implant designs, Newclip Technics was faced with the question of how to optimise the management of high-volume, fast-track osteosynthesis cases in the operating theatre.
Traumatology is synonymous with urgency, and it is sometimes difficult to respond quickly to large patient flows with implants and instruments traditionally offered in containers requiring sterilisation in the operating theatre. The handling time and logistics inherent in this type of material naturally lead to a high frequency of patient rotation in the OR.
Inspired by sectors such as cardiology and ophthalmology, the Initial Solutions concept was launched. It consists of offering single-use sterile kits in blister packs, ready to use, with the latest generation of implants and associated instruments. In 2013, Newclip Technics became the first osteosynthesis company to introduce these kits to the market, with its range for the treatment of wrist fractures: Initial R.
Today, this range includes solutions for the clavicle, wrist, hand, knee, ankle and foot. It has become one of the company’s best-sellers.
Combining our historical roots with cutting-edge technology
After numerous discussions with surgeons, the question of the democratization of knee osteotomies arose, an operation requiring a certain amount of experience, for the surgical technique and for the planning beforehand. Newclip Technics has therefore endeavoured to structure and build a genuine service to support the surgeon in these areas. By developing pre-operative simulation solutions applied to the imaging of the patient to be treated, and then by proposing customised instrumentation (cutting guides) intended to faithfully reproduce the previously simulated operation, Newclip Technics has been able to establish a division known as “PSI” (Patient Specific Instrumentation).
With the contribution of 3D printing, its teams of engineers and CAD technicians, and its medical imaging operators, Newclip Technics is helping to make complex bone correction procedures accessible and safe. The core of this service is to provide the surgeon with better tools to restore the patient’s functional anatomy as best as possible.
After several years of practice, this PSI division, now called One, is able to offer its know-how in several osteoarticular areas (upper limb, lower limb, foot and ankle, etc.).
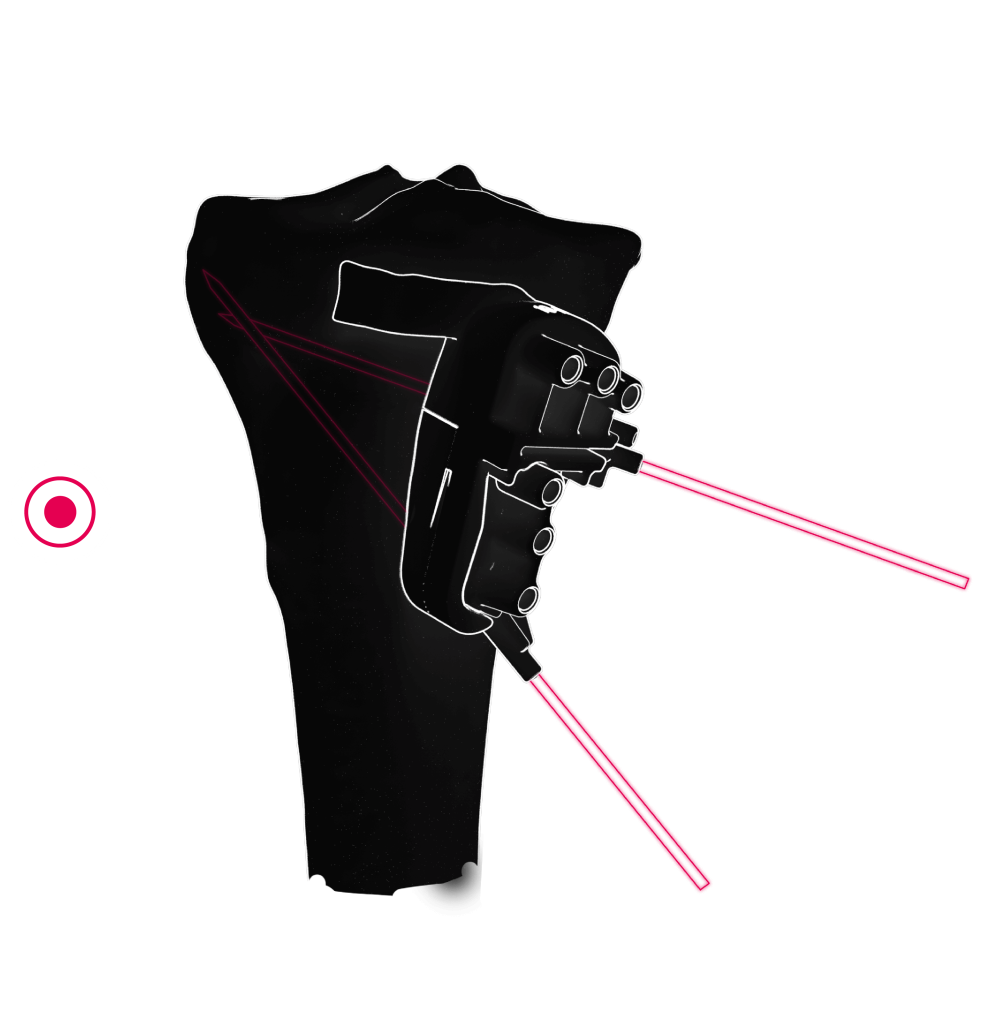
Our expertise
Since 2001, our SME has had several addresses, starting with a small 30m2 office in the north of Nantes, within the Atlanpôle industrial park. Today the company is based in Haute-Goulaine, still in the suburbs of Nantes, and has 3 sites to be able to control the vast majority of its industrial processes and other support services linked to its activity. This French quality is applied to all its products through:
- Newclip Technics (2 200 m2)
- Newclip Packaging (600 m2)
- Newclip Manufacturing (2 700 m2)
The geographical proximity of the three sites means that the same quality of execution can be shared, from conception through manufacturing to distribution.
Each department works closely with the others to ensure a quality product that meets the needs of the markets. Each building symbolises the independence of the company and the mastery of its savoir-faire.
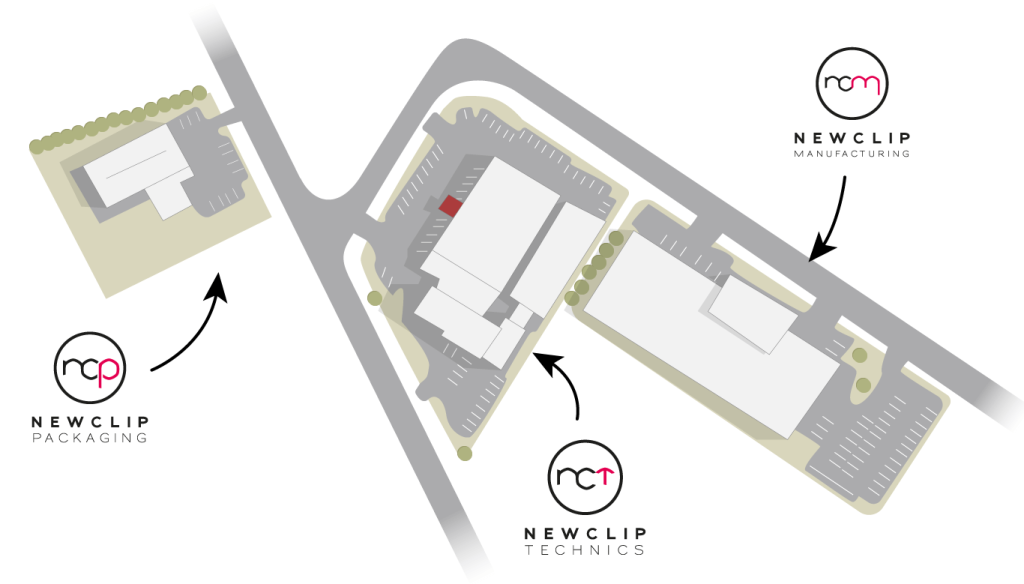
Newclip Technics
Established since 2012. In Haute Goulaine, Newclip Technics originally housed the offices, the warehouse and manufacturing site.
Since 2019, this building is dedicated to support services and its logistics platform (including PSI)
and employs approximately 180 people.

Newclip Packaging
The emergence of its Initial Solutions range led Newclip Technics to rapidly integrate the businesses related to cleaning,
surface treatment and packaging in clean rooms.
Newclip Packaging was founded in 2016, has around 20 employees and handles the entire finishing process for the company’s products,
whether they are marketed as sterile or non-sterile.

Newclip Manufacturing
In 2002, Newclip acquired its first CNC machine. The company’s production facilities have expanded considerably
over the years (bar turning, high-speed milling, injection moulding, etc.),
this led to the creation of a dedicated unit, called Newclip Manufacturing, which opened its doors in 2019.
Control of the industrial tool has always been at the heart of the company’s project and competitiveness,
as the first guarantee of its independence. Today, Newclip Manufacturing employs around 40 people.
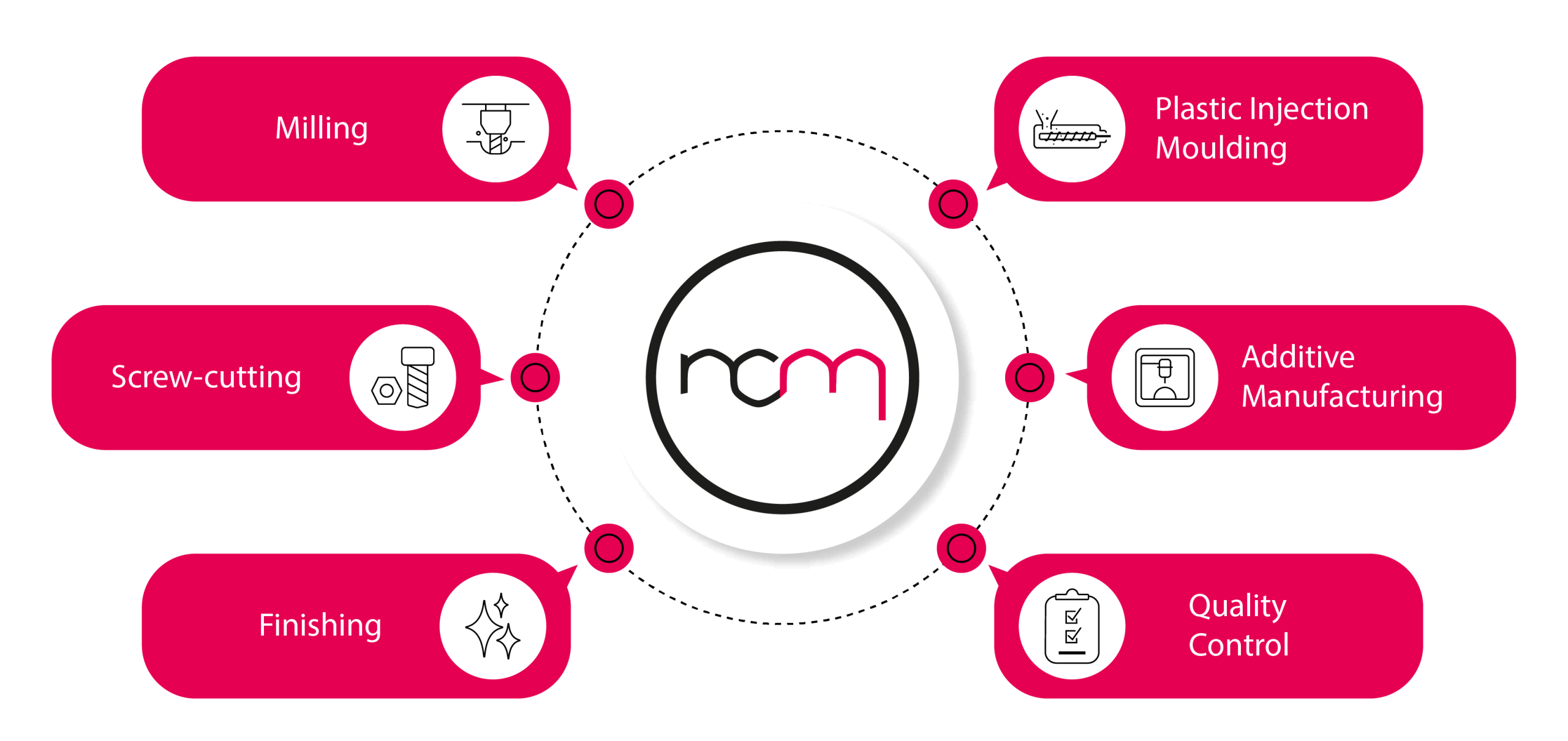
All this expertise combined allows for an exchange of know-how, quality of execution and perfect control of the product, from its conception to its sale.
Certifications
We operate in a world where medical companies are governed by international standards and regulations that define good practice. Our teams are regularly audited, and the conformity of our products is analysed, controlled and certified by independent organisations, before they can be put on the market.
Newclip Technics is proud to be one of the first European companies to receive CE certification for all its products under the new MDR regulation (EU 2017/745), and via the ISO 13485 standard.
In addition to being present on the European market, Newclip Technics distributes its solutions in more than 40 countries around the world, and must therefore comply with the regulatory certifications of these different countries, including the FDA (USA), the MHLW (Japan), the ANVISA (Brazil…).
Environment
Even if the mission of Newclip Technics remains the optimisation of the surgical gesture and the benefit for the patient, the preservation of the environment is also at the heart of the company’s concerns. From the outset, Newclip Technics has focused on the use of renewable energy and the recycling of its industrial waste to reduce its carbon footprint, and is working to ensure that its activities preserve the world of tomorrow. Today, these commitments are recognised by:
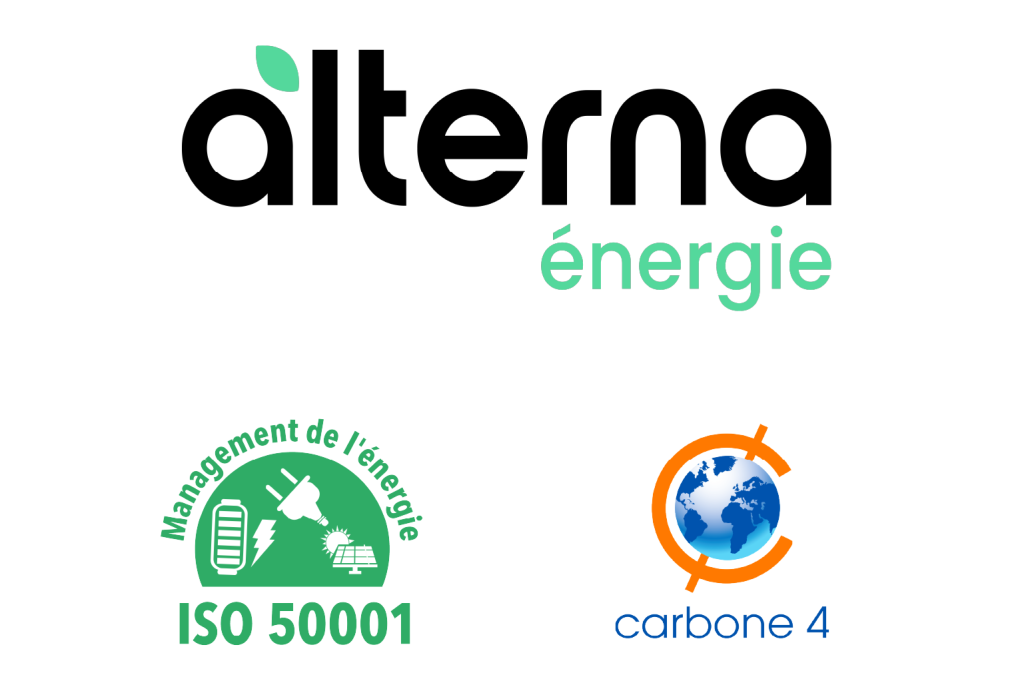
Our global presence
To innovate further, it was obvious for Newclip Technics to offer our products abroad. Understanding these markets has led us to develop a complete and unique portfolio of products that are attractive both internationally and in France.
Newclip Technics has a strong worldwide presence with 3 subsidiaries on the European continent and 3 others on the other side of the world:
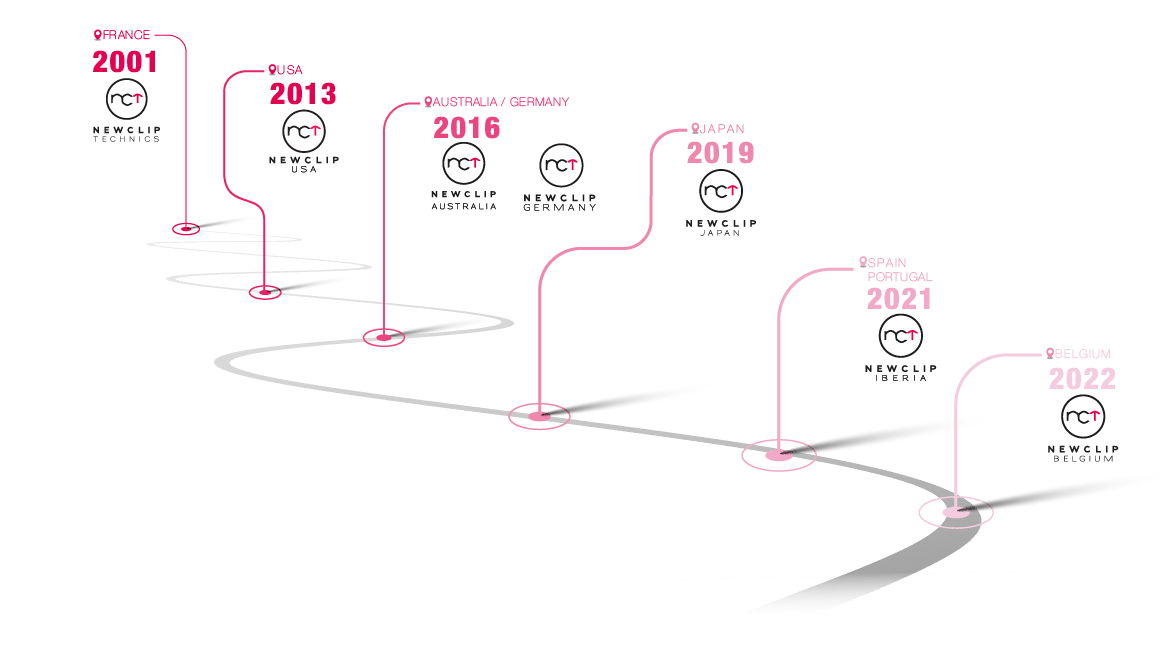
With the help of our subsidiaries and our strong network of distributors, today our products are distributed in 50 countries worldwide.
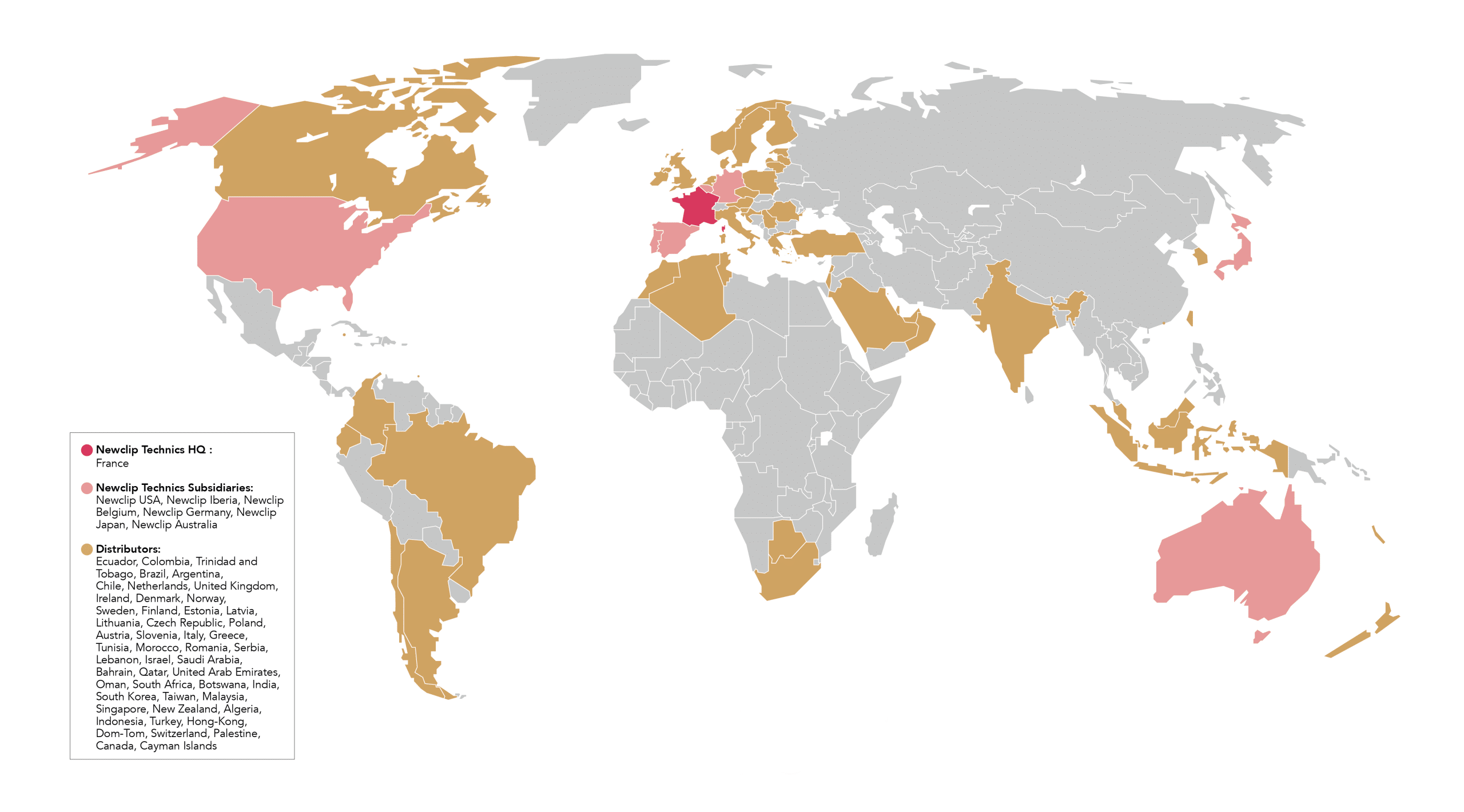
Newclip Faculty
For Newclip Technics, education is a must. In addition to marketing osteosynthesis solutions,
we offer surgeons the opportunity to be trained on our new techniques and products.
All of our experts are chosen for their technical expertise, educational quality and reputation.
Newclip Faculty events are a combination of lectures, case discussions, and practice on anatomical subjects.
Find out more about Newclip Faculty